Industrial Wired Connectivity Technology
Today, wired connectivity technology remains the primary technology adopted in the industrial sector. Existing factory networks widely utilize legacy serial interfaces to ensure uninterrupted high-performance connections. These interfaces are simple and user-friendly but lack the direct IP addressing advantages of Ethernet, which is the main technology used at the control layer. Additionally, in the future, there is likely to be a coexistence of new and old equipment in factory environments, and new wired connectivity technologies will facilitate interoperability between them.
ADI's wired connectivity solutions leverage both new serial and Ethernet technologies to deliver outstanding performance, reliability, and coverage. They enable the last-mile connection to edge sensors or actuators using 10BASE-T1L and IO-Link®. For high-speed applications, low-latency Gigabit Ethernet, MLVDS, and RS-485 can be employed. ADI also offers highly reliable, next-generation isolated USB solutions for industrial PC connections.
Industrial Ethernet
Optimize system design and enhance Ethernet connections with low-power, low-latency, and reliable Gigabit PHY, MAC PHY, and switch technologies. Immediately adopt ADI's pre-certified multi-protocol 100 Mbit connection reference designs to build dual-port device connectivity solutions.
IO-Link Solutions
Build intelligent connected sensors and actuators that support IO-Link, devices that can auto-identify and configure, reducing configuration and debugging time. ADI offers advanced, reliable solutions with enhanced functionality support, along with a range of thoroughly certified and tested reference designs.
Serial Connectivity Solutions
Choose from isolated and non-isolated RS-485, RS-232, RS-422, RS-562, and CAN transceivers, all utilizing ADI's iCoupler® and isoPower® isolation technologies, for reliable, noise-immune network connections in harsh industrial environments.
Isolated USB Solutions
Compact USB port isolators that, for the first time, support USB 2.0 high-speed operation and higher reliability in high-bandwidth applications like smart industry, digital health, and instrumentation. Learn how these USB isolators easily integrate into designs to achieve signal integrity, EMC compliance, and the proven reliability of iCoupler.
Selected Technologies for the Future Factory
Industrial Ethernet
ADIN1300
Reliable, industrial, low-latency, and low-power 10 Mbps, 100 Mbps, and 1 Gbps Ethernet PHY
Isolated USB
MAX22514
Surge-protected low-power IO-Link transceivers with efficient DC-DC conversion
RS-485
ADM2867E
5.7 kV RMS signal and power isolated RS-485 transceiver with ±15 kV IEC ESD protection
Why Choose ADI for IO-Link?
ADI offers a complete range of IO-Link gateway and sensor devices and possesses domain expertise to help build low-power, efficient IO-Link platforms. Utilize validated designs to develop solutions quickly and easily, or explore ADI's evaluation kits that come with configuration software to expedite system setup. ADI's solutions are compact and highly reliable, eliminating the need for multiple external protection components, reducing system size by up to 50%.
More Application-Related Electronic Components
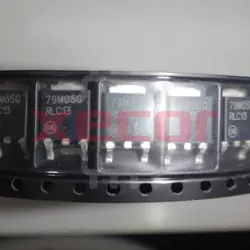
MC79M05CDTRKG
Linear regulators with negative feedback designed to provide a constant 5V output at a maximum current of 500mA

KSZ8895MQXIA
High-speed networking switch
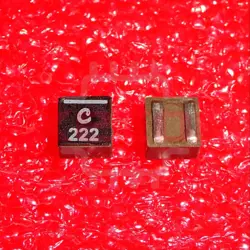
XGL4030-222MEC
2.2uH ±20% 7A 1616 Power Inductors ROHS
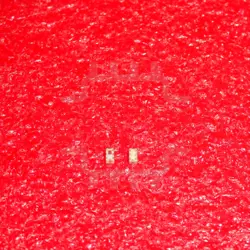
0900LP15B0063E
Ceramic Filters Low Pass 900MHz 0.9dB 50Ohm SMD 8Pin T/R
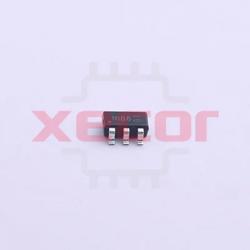
ZXMN10B08E6TA
ZXMN10B08E6TA is a N Channel MOSFET, featuring a voltage rating of 100V and a maximum current of 1.6A, with a low on-resistance of 230mΩ at 10V

ZXMN6A07FTA
Small Signal Field-Effect Transistor

MLX90614ESF-DCI-000-TU
Digital Temperature Sensor MLX90614ESF-DCI-000-TU, Operating Range: -40°C to 85°C, TO39 Enclosure
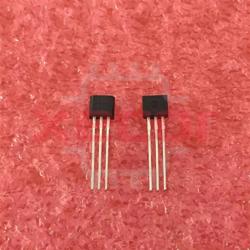
ZVN2106A
channel MOSFET with a voltage rating of 60V, current rating of 0.45A, and power dissipation of 0.7W, packaged in TO92
READ ALSO
-
Industrial Wireless Connectivity Technology Date: 08/10/2023
Wireless communication has been used in industrial applications for many years, initially for basic control of cranes and other mobile equipment. With the adoption of more standardized wireless connectivity technologies in recent decades, control has expanded to a wider range of terminal devices.
-
Industrial Wired Connectivity Technology Date: 08/10/2023
Today, wired connectivity technology remains the primary technology adopted in the industrial sector. Existing factory networks widely utilize legacy serial interfaces to ensure uninterrupted high-performance connections.
-
Vibration Detection for Condition Monitoring Date: 08/10/2023
As manufacturers seek to improve throughput and asset utilization by reducing maintenance costs and asset downtime, real-time continuous condition monitoring and predictive maintenance solutions become increasingly important. Given that the cost of unplanned downtime can account for nearly one-fourth of total manufacturing costs, adopting predictive maintenance solutions has the potential to significantly save costs and boost productivity.