Our business foundation rests upon diligence, meticulous processes, and unwavering attention to detail.
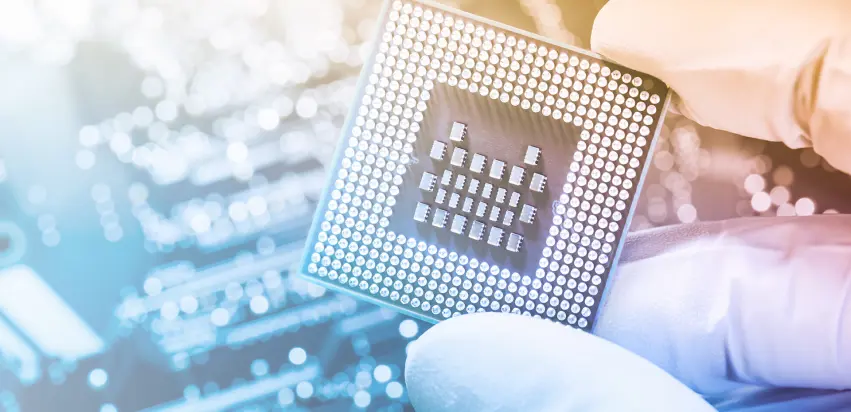
Four Pillars of QC System
As a core strength of our company, we have built dedicated QC system committed to ensuring the excellence and reliability of electronic components. In the process of electronic component quality testing, we focus on the following four key aspects:
Visual and Dimensional Inspection
Our experts conduct a thorough examination of the appearance of each component, ensuring there are no physical damages or contaminants. Additionally, precise dimensional measurements are integral to ensuring components meet specified standards.
Performance and Function Verification
Equipped with advanced testing equipment, we are capable of comprehensively verifying the performance and functions of components. Through rigorous testing protocols, we ensure each component performs reliably in real-world applications.
Material and Composition Analysis
Our team employs cutting-edge analytical instruments to perform detailed analyses of the materials and compositions used in components. This ensures that the materials utilized in components adhere to standards, enhancing overall quality and reliability.
Environmental and Reliability Testing
To simulate diverse operating environments, we conduct testing under various conditions such as high temperatures, low temperatures, and humidity. These tests validate the stability and reliability of components in different scenarios.
Through our self-established QC system, we guarantee that each electronic component undergoes rigorous scrutiny to meet the high-quality standards of various industries. We understand that quality is pivotal to your trust in us, and as such, we continue to invest resources to provide you with the most dependable electronic components.
We conduct a thorough assessment, measurement, validation, and testing process on electronic components starting from the external packaging, ensuring they adhere to the most stringent quality criteria.
Visual Inspection
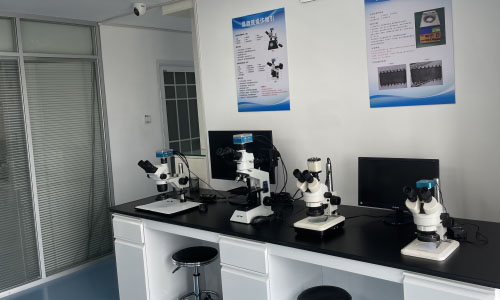
From a professional perspective on electronic components, visual inspection is a key step. Through careful observation, we ensure that the external appearance of components is undamaged. The inspection covers integrity, clear labeling, soldering connections, color coatings, contamination, and external deformities. Through rigorous examination, we ensure the provision of high-quality and reliable components.
Acetone Testing
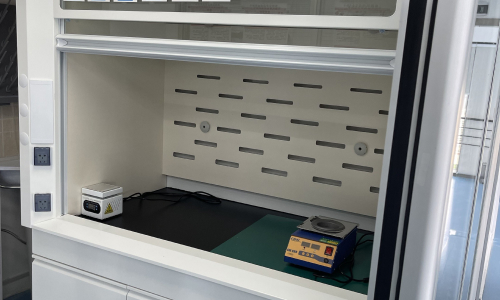
Acetone testing is a vital method for quality assessment of electronic components, particularly in the realm of electronic manufacturing. By applying a small amount of acetone to the surface of a component, we can observe its reaction with materials to detect potential issues. This testing aids in verifying external appearance, material quality, and reliability of components, while also predicting long-term performance. However, it's crucial to conduct this test in a controlled environment to prevent unnecessary damage.
X-Ray Inspection
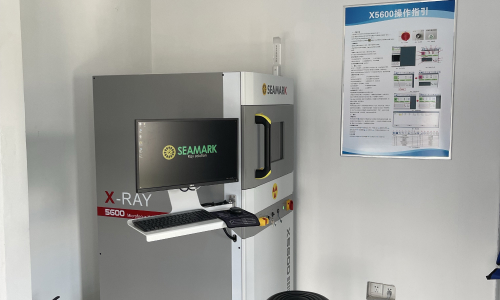
X-ray inspection, viewed from the perspective of electronic components professionals, is a critical quality assessment method. By utilizing X-rays, we can non-invasively explore the internal structures and connections of components. This technique reveals welding issues, internal defects, and material distributions. X-ray inspection plays a significant role in ensuring component quality, reliability, and performance, aiding manufacturers in delivering high-quality electronic products.
Decapsulation
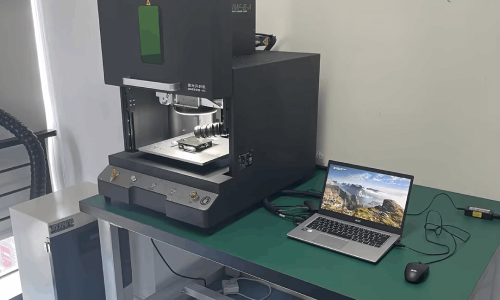
Decapsulation testing is a crucial quality assessment method in the field of electronic components. It involves dismantling the packaging to reveal internal structures and components, aiding in verifying authenticity, reliability, and manufacturing quality. While effective, this method should be conducted in a professional environment to prevent damage and mishandling.
XRF/EDS
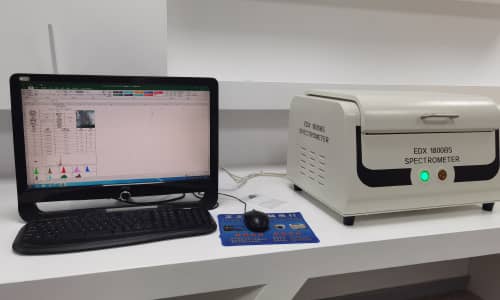
XRF (X-ray Fluorescence) and EDS (Energy Dispersive X-ray Spectroscopy) are commonly used analytical tools in the field of electronic components, employed for material composition analysis. By emitting X-rays and identifying elements within a sample, these techniques rapidly and accurately determine the chemical makeup of components. In quality control and failure analysis, XRF and EDS offer insights into component composition, ensuring product quality and performance.
Dedicated to the excellence of every sourced product, we maintain a steadfast commitment to quality.
Our expert quality inspectors are well-versed in the latest techniques for detecting and preventing fraud and counterfeits.
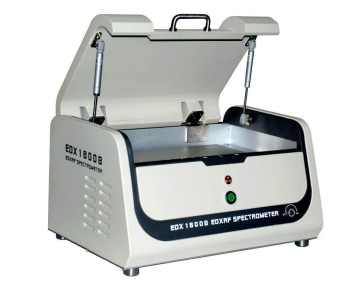
RoHS Testing
RoHS testing is a vital environmental assessment method in the electronic components industry, used to verify if components comply with the Restriction of Hazardous Substances Directive. This testing helps ensure products are free from harmful substances, safeguarding the environment and user health. It should be conducted in a professional laboratory setting for accuracy and reliability.
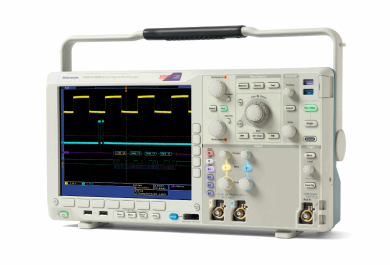
Key Functionality Testing
Key functionality testing is a critically important quality validation method in the field of electronic components. It aims to confirm the proper operation of the essential functions of components. By simulating real-world usage scenarios, we can verify whether components perform well and remain stable under specific conditions. This testing helps ensure that components function as expected in practical applications, meeting customer requirements.
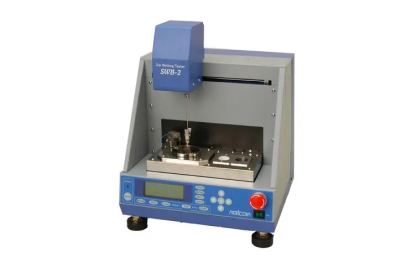
Solderability Testing
Solderability testing plays a significant role in the field of electronic components, aiming to validate the performance of components during the soldering process. This testing helps ensure that components can be effectively soldered onto PCB boards, ensuring manufacturing quality and stability. By simulating various soldering conditions and evaluating soldering performance and outcomes, we ensure reliable connections of components in practical applications.
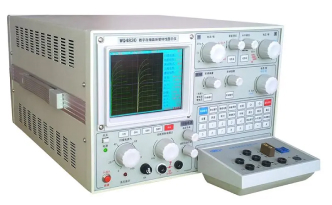
Electrical Performance Testing
Electrical performance testing is a vital quality assessment method in the field of electronic components, aimed at evaluating the electrical characteristics of components. By measuring parameters like voltage, current, and resistance, we can verify the electrical performance of components under various conditions. This testing helps ensure the stability and reliability of components in diverse application scenarios, safeguarding the proper operation of devices.