Automated Testing Solutions for Automotive Electronic Control Units (ECUs) Based on VT (Vector Test) System
This article begins by outlining the current state of testing for automotive Electronic Control Units (ECUs) and then delves into the execution process of ECU automation testing using the VT (Vector Test) system, including bus simulation, analysis tools like CANoe, and more. It serves as a reference for planning and executing ECU testing strategies.
Current Testing Landscape
As automotive ECUs become more complex in terms of functionality and network integration, a delicate balance between quality, cost, and development time poses numerous testing challenges for both automakers and suppliers. For test engineers, the need for efficient testing has become increasingly critical, demanding new requirements for ECU testing platforms and test case development.
Challenges for Test Engineers
Presently, test engineers face a growing number of challenges, primarily in two areas:
- Transitioning from manual testing to automated testing.
- Managing an increasing number of test projects.
Focus Areas for Test Engineers
Test engineers are primarily concerned with the following aspects:
- Whether the testing platform can meet the requirements for fault testing.
- The platform's versatility across new projects.
- The platform's scalability.
Using an ECU automation testing platform improves testing efficiency, accuracy, and consistency. It allows test personnel to focus on defining front-end test specifications and analyzing back-end test results. By refining the testing development process, you can build and manage a test library and test data, ensuring the reusability of testing assets and the scalability of the testing platform.
Trends in Automotive ECU Automation Testing
Compared to manual testing, automation testing offers several distinct advantages, including faster execution of test cases, higher testing accuracy, and greater reusability.
A typical approach to automotive ECU automation testing involves simulating the peripheral components surrounding the ECU, such as residual bus systems, sensors, and actuators. This approach essentially creates a closed-loop simulation environment, where the ECU's behavior under specific test conditions is observed while simulating the ECU's working environment.
This type of testing requires functionalities like bus simulation, sensor and actuator simulation, I/O emulation, and scripted testing. All these functionalities can be effectively achieved using Vector's testing toolchain.
In summary, ECU automation testing based on the VT system, CANoe software, vTESTstudio test case development tool, VN series interface cards, and VT testing system offers an efficient and cost-effective means to conduct comprehensive testing of ECUs. It not only improves testing efficiency but also effectively reduces testing time and labor costs.
Vector Testing Toolchain
Vector provides a comprehensive toolchain for various ECU testing purposes. The workflow based on the Vector testing toolchain is depicted in the figure below:
Workflow based on the Vector testing toolchain
1. CANoe:
CANoe is an integrated automotive network development software platform that combines bus simulation, logging, and testing capabilities. It offers strong support for building testing systems and automating the testing process. CANoe includes features such as network communication and high-level protocol simulation, test process logging, test script generation, test panel development, integration of test modes and function libraries, and more. CANoe also provides flexible test panel design capabilities, allowing users to intuitively control the testing process and monitor the status of the units under test. CANoe supports various automotive bus types, including CAN, LIN, FlexRay, MOST, J1939, Ethernet, and more.
2. Vector VT Hardware Testing System:
Vector's VT hardware testing system features a modular design and offers a wide range of optional I/O cards for simulating input signals to the Device Under Test (DUT) and detecting its outputs. It also includes current measurement interfaces and control interfaces for power supplies. The VT cards are highly integrated and come with built-in signal conditioning modules, meeting the automotive industry's requirements for signal simulation and acquisition. Some VT cards also offer built-in fault injection capabilities to meet diagnostic testing requirements. The VT hardware testing system seamlessly integrates with CANoe, providing comprehensive coverage for network testing needs, including interaction layer, network management, diagnostic protocols, and more.
3. vTESTStudio Test Case Development Software:
vTESTStudio is a test case development software that offers a script-based, flowchart-based, and tabular-based development interface. It also integrates features for requirements management, variant management, and defect tracking. With vTESTStudio, users can easily develop and maintain test cases, create and edit test sequences, define the execution order of test cases, use elements from CAN, LIN, FlexRay databases (DBC, LDF, FIBEX), and use elements from diagnostic databases (CDD, ODX). It allows graphical parameterization of test modes, linking, and modification of test cases from the CAPL library, and outputs test lists in the form of test specifications for review and inspection.
In summary, the Vector testing toolchain, comprising CANoe, the Vector VT hardware testing system, and vTESTStudio, provides a powerful and integrated solution for ECU testing. It covers a wide range of testing needs, including network simulation, signal conditioning, fault injection, and test case development, facilitating efficient and accurate ECU testing processes.
Testing System Components
The architecture of the ECU automated testing platform based on the VT system is depicted in the figure below:
Architecture of the ECU automated testing platform based on VT
Test Cases: Test cases are developed based on the relevant testing specifications and can be implemented using CAPL, vTESTStudio, or CANoe.DiVa. vTESTStudio, in particular, offers technical advantages in improving test case development efficiency and coverage.
CANoe: CANoe provides the testing execution and management environment.
VT System: The VT system is a modular hardware platform for simulating and testing I/O signals. It can simulate sensors, actuators, and other external devices.
PicoScope: PicoScope is a bus oscilloscope used to record and analyze the physical bus levels. It seamlessly integrates with CANoe.
CANStressDR: CAN bus disruptor that can simulate analog and digital interference, suitable for bus consistency testing.
Other Devices: These devices are used to create the controller's working and testing environment, including programmable power supplies, breakout boxes (BOB), and more.
Conclusion
As vehicle Electronic Control Unit (ECU) functionality and network complexity increase, the workload for testing engineers also continues to grow. Testing engineers need to carry out relevant tests and verifications according to their specifications. However, traditional testing methods often face the following challenges:
Low Testing Efficiency: Traditional testing typically involves a significant amount of manual testing, consuming a considerable amount of testing personnel's time.
Low Test Coverage: Traditional methods may struggle to achieve dynamic functional testing, function matching testing, or simulate extreme and fault conditions adequately.
Low Reusability and Scalability: Traditional methods may have limited adaptability to different variants of controllers.
As testing requirements continue to expand, traditional testing technologies and methods may become inadequate. ECU automated testing systems simulate drivers, vehicles, and their operating environments, making them a mainstream approach for automated ECU testing. They offer the following advantages:
Test Coverage: They facilitate the simulation of various conditions, combinations of input signals, and complex fault modes.
Efficiency: ECU automated testing systems enable efficient automation of testing, accumulate and reuse testing development results, and reduce redundant development efforts.
System Reusability: They can adapt to different controller variants, and the systems are easy to maintain and expand.
Overall, ECU automated testing systems address the shortcomings of traditional testing methods and offer improved efficiency, coverage, and scalability, making them a valuable solution for modern ECU testing challenges.
More Application-Related Electronic Components

PEX8605-AB50TQI G
PCI Interface IC 4 Lane/4 Port PCIe Gen 2.0 Switch

BTS660P-E3180A
Power switch driver

PEX8624-BB50RBC G
PCI Interface IC PCIe Gen2 5.0GT/s 24-Lane 6 Port

PEX8724-CA80BC G
PCI Interface IC GEN 3 PCIe Switch 24 Lane, 6 Port
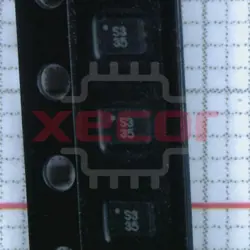
SKY13335-381LF
Gallium arsenide IC with a single pole and double throw configuration designed for frequency switching between 0

DSS1NB32A271Q55B
EMI Filter LC-Circuit 6A 100VDC RDL Thru-Hole Automotive AEC-Q200 Bag
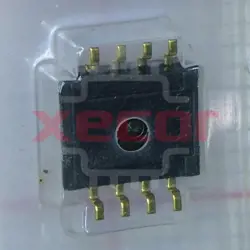
CHS-04B
Switch Slide OFF ON 4PST Recessed Slide 0.1A 24VDC Gull Wing SMD Bulk
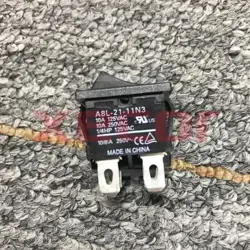
A8L-21-11N3
Rocker Switches
READ ALSO
-
Automotive OTA Automated Testing Solutions Date: 26/09/2023
OTA technology is one of the symbols of automobile intelligence, and OTA upgrades continue to provide customers with New features continuously enhance user experience.
-
Vehicle Bus Data Recorder Solution Date: 26/09/2023
CAN and LIN bus records are important tools for automotive engineers in fault diagnosis, performance analysis and data recording, helping engineers gain an in-depth understanding of the working principle of the vehicle and the interaction between various electronic control systems.
-
Central computing electronic and electrical architecture solutions Date: 26/09/2023
In the era of intelligent and software-defined cars, whoever can dominate the EE architecture and software can occupy the commanding heights of the smart car market. Therefore, domestic mainstream vehicle companies are also actively making relevant layouts, and mass-produced models with "quasi-centralized" architecture solutions will be launched around 2022-2023.